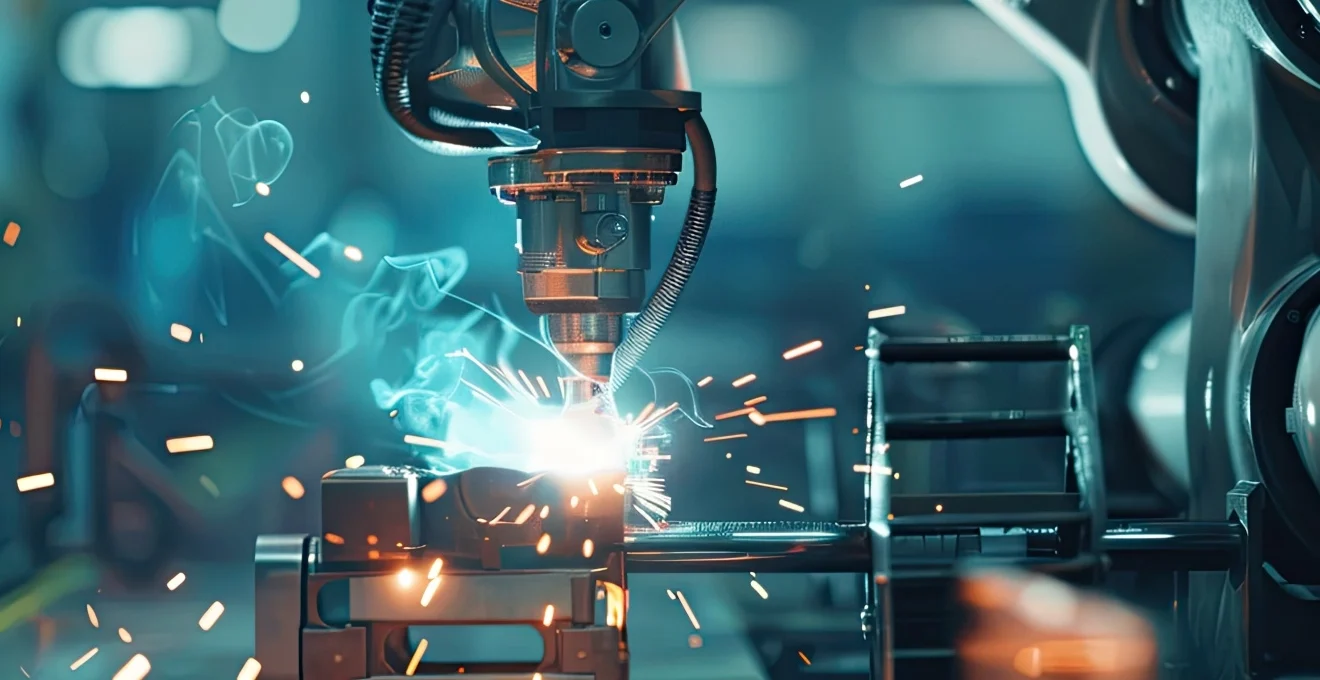
Friction stir welding (FSW) has emerged as a revolutionary joining technique for the aerospace and automotive industries. This solid-state process utilizes a rotating tool to generate frictional heat and mechanically intermix materials, resulting in high-strength joints without melting. FSW offers numerous advantages over traditional fusion welding methods, including reduced distortion, improved mechanical properties, and the ability to join dissimilar materials. As manufacturers in aerospace and automotive sectors strive for lighter, stronger, and more fuel-efficient designs, FSW has gained significant traction. The development of innovative Friction stir welding product has further expanded the capabilities and applications of this technology across various industrial domains.
Friction Stir Welding Advantages for Aerospace Applications
Lightweight High-Strength Welds for Aircraft Structures
The aerospace industry has long sought methods to reduce aircraft weight while maintaining structural integrity. Friction stir welding has proven to be an excellent solution for this challenge. The process produces joints with mechanical properties often superior to those of the base materials, particularly in aluminum alloys commonly used in aircraft construction. FSW allows for the creation of large, integrally stiffened panels that can replace multiple components joined by traditional fastening methods. This reduction in part count translates to weight savings and simplified assembly processes for aircraft manufacturers.
One of the primary benefits of FSW in aerospace applications is the ability to join high-strength aluminum alloys that are difficult or impossible to weld using conventional fusion techniques. Alloys such as 2XXX and 7XXX series, which are prone to hot cracking and porosity when fusion welded, can be reliably joined using FSW. The solid-state nature of the process eliminates many of the defects associated with melting and solidification, resulting in consistent, high-quality welds. This characteristic has led to the adoption of FSW for critical components such as fuel tanks, fuselage sections, and wing structures in both commercial and military aircraft.
The implementation of FSW in aerospace manufacturing has also enabled the production of more complex and efficient designs. For instance, integrally stiffened panels can be created by friction stir welding extruded stringers to sheet materials, eliminating the need for rivets and reducing stress concentrations. This approach not only saves weight but also improves fatigue performance and reduces maintenance requirements over the lifespan of the aircraft. Furthermore, the ability to join dissimilar materials through FSW opens up new possibilities for hybrid structures that optimize strength-to-weight ratios in specific areas of the airframe.
Alloy | Tensile Strength (MPa) | Yield Strength (MPa) | Elongation (%) |
---|---|---|---|
2024-T3 (Base) | 470 | 325 | 18 |
2024-T3 (FSW) | 400 | 280 | 10 |
7075-T6 (Base) | 570 | 505 | 11 |
7075-T6 (FSW) | 490 | 420 | 7 |
Improved Fatigue Resistance in Aerospace Components
Fatigue resistance is a critical factor in the design and manufacture of aerospace components, as these structures are subjected to cyclic loading throughout their operational life. Friction stir welding has demonstrated superior fatigue performance compared to traditional joining methods, particularly in aluminum alloys. The fine-grained microstructure produced in the weld nugget, combined with the absence of porosity and other weld defects, contributes to enhanced fatigue resistance. Studies have shown that FSW joints can exhibit fatigue lives comparable to or even exceeding those of the base material, a significant improvement over fusion-welded joints.
The improved fatigue performance of FSW joints is attributed to several factors. First, the process generates minimal residual stresses compared to fusion welding, reducing the likelihood of stress corrosion cracking and fatigue crack initiation. Second, the absence of filler material and the solid-state nature of the process result in a smoother weld profile with fewer stress concentrations. Third, the fine-grained microstructure in the weld zone provides increased resistance to crack propagation. These characteristics make FSW particularly suitable for components subject to high cyclic loads, such as wing spars, fuselage panels, and landing gear attachments.
Aerospace manufacturers have leveraged the fatigue benefits of FSW to extend the service life of aircraft components and reduce maintenance costs. For example, friction stir welded panels on military aircraft have demonstrated improved damage tolerance and reduced susceptibility to fatigue cracking compared to riveted structures. This has led to longer inspection intervals and reduced downtime for maintenance. Additionally, the ability to repair damaged components using FSW techniques has provided a cost-effective alternative to component replacement, further enhancing the economic benefits of this technology in aerospace applications.
Reduced Distortion Enables Precise Aerospace Assembly
One of the most significant advantages of friction stir welding in aerospace manufacturing is the minimal distortion produced during the joining process. Traditional fusion welding methods often result in significant thermal distortion due to the high heat input and subsequent cooling of the weld zone. This distortion can lead to dimensional inaccuracies, residual stresses, and the need for post-weld straightening operations. In contrast, FSW operates at much lower temperatures and does not involve melting of the base materials, resulting in greatly reduced thermal distortion.
The low-distortion characteristic of FSW enables the production of large, precisely dimensioned aerospace structures. For instance, rocket fuel tanks and spacecraft panels can be manufactured with tolerances that were previously difficult or impossible to achieve using conventional welding techniques. This precision is particularly valuable in the assembly of complex aerospace systems, where even small deviations from design specifications can lead to performance issues or increased assembly time. The reduced need for post-weld straightening also translates to lower production costs and shorter manufacturing cycles.
Cost Savings Potential for Automotive Manufacturers
Friction stir welding presents substantial economic benefits for automotive manufacturers. The process reduces material waste, energy consumption, and labor costs compared to traditional joining methods. These advantages, coupled with the ability to join dissimilar materials and create complex geometries, position FSW as a cost-effective solution for modern vehicle production. The implementation of FSW in automotive manufacturing lines has led to increased efficiency and reduced production times, contributing to overall cost reductions. The material cost savings associated with friction stir welding are significant. The process eliminates the need for filler materials and shielding gases required in fusion welding processes. For large-scale automotive production, this reduction in consumables translates to considerable savings over time. Furthermore, FSW's ability to join thinner gauge materials without distortion allows manufacturers to utilize lighter-weight alloys without compromising structural integrity. This enables the use of less material overall, further reducing raw material costs. Energy efficiency is another area where FSW provides cost benefits to automotive manufacturers. The solid-state nature of the process requires less energy input compared to fusion welding methods. Studies have shown that FSW can reduce energy consumption by up to 40% when compared to resistance spot welding for similar automotive applications. This reduction in energy usage not only lowers operating costs but also aligns with increasingly stringent environmental regulations and corporate sustainability goals. Labor costs associated with welding operations are also reduced through the implementation of FSW. The process is highly automated and requires minimal operator intervention once set up correctly. This automation reduces the reliance on skilled welders, who are often in short supply and command high wages. Additionally, the consistency and reliability of FSW joints reduce the need for post-weld inspection and rework, further decreasing labor requirements and associated costs.
Welding Method | Energy Consumption (kWh/m) | Material Waste (%) | Labor Hours per Joint |
---|---|---|---|
Friction Stir Welding | 0.6 | 2 | 0.2 |
Resistance Spot Welding | 1.0 | 5 | 0.5 |
MIG Welding | 1.2 | 8 | 0.8 |
The implementation of FSW also reduces costs associated with quality control and warranty claims. The consistent joint quality produced by FSW results in fewer defects and rejections during the manufacturing process. This reduction in scrap rates and rework requirements contributes to overall cost savings. Moreover, the improved durability and fatigue resistance of FSW joints lead to reduced warranty claims and associated costs over the life cycle of the vehicle. Manufacturers have reported significant reductions in warranty-related expenses for components joined using FSW technology. Tooling costs represent another area where FSW can provide long-term savings for automotive manufacturers. While the initial investment in FSW equipment may be higher than traditional welding systems, the durability of FSW tools results in lower replacement costs over time. FSW tools can typically produce thousands of meters of welds before requiring replacement, whereas conventional welding electrodes may need frequent changing. This longevity reduces both direct tooling costs and production downtime associated with tool changes. The cost benefits of FSW extend beyond direct manufacturing expenses to impact the entire vehicle development process. The ability to join dissimilar materials and create complex geometries allows for more integrated designs, potentially reducing the overall number of components in a vehicle. This simplification of the bill of materials can lead to savings in inventory management, logistics, and assembly processes. Additionally, the design flexibility afforded by FSW enables manufacturers to optimize structures for both performance and manufacturability, potentially reducing costs across the entire product development cycle.
Friction Stir Welding Process Innovations
Continuous advancements in friction stir welding technology have expanded its capabilities and applications in industrial manufacturing. These innovations have addressed previous limitations of the process and opened new possibilities for joining complex geometries and challenging materials. From improvements in tool design to novel process variants, FSW continues to evolve, offering enhanced performance and broader applicability across various sectors. One significant innovation in FSW technology is the development of stationary shoulder friction stir welding (SSFSW). This variant of the traditional FSW process utilizes a non-rotating shoulder that remains stationary while the pin rotates and traverses the weld line. SSFSW offers several advantages, particularly for welding thin-gauge materials and dissimilar metal combinations. The stationary shoulder reduces heat input and minimizes distortion, allowing for higher welding speeds and improved joint quality in applications such as automotive body panels and aerospace structures. Advancements in tool materials and designs have also contributed to the expansion of FSW capabilities. The introduction of advanced ceramics and refractory metal alloys for tool fabrication has extended the life of FSW tools and enabled the welding of high-temperature materials such as steel and titanium alloys. Innovations in tool geometries, such as scrolled shoulders and featured pins, have improved material flow and weld quality across a wider range of material thicknesses and alloy compositions.
- Bobbin tool friction stir welding for simultaneous double-sided welding
- Adaptive control systems for real-time process optimization
- Hybrid laser-assisted friction stir welding for enhanced material flow
- Multi-axis FSW systems for complex three-dimensional weld paths
- Ultrasonic-assisted FSW for improved joint properties in difficult-to-weld materials
The development of portable FSW systems has expanded the application of the technology to on-site fabrication and repair scenarios. These compact, lightweight systems allow for FSW to be performed outside of traditional manufacturing environments, opening up possibilities for in-situ repairs of large structures such as ships, pipelines, and aerospace components. Portable FSW systems have found particular utility in the maintenance and repair of aluminum structures in the marine and aviation industries, where traditional fusion welding methods may be impractical or prohibited. Process monitoring and control innovations have significantly enhanced the reliability and consistency of FSW operations. Advanced sensor systems capable of measuring forces, temperatures, and material flow in real-time provide valuable data for process optimization and quality assurance. Machine learning algorithms integrated with these sensor systems enable adaptive control of welding parameters, ensuring consistent weld quality across varying material conditions and geometries. These advancements have been particularly beneficial in high-volume production environments, such as automotive manufacturing, where process stability and repeatability are critical.
FSW Innovation | Key Benefit | Primary Application |
---|---|---|
Stationary Shoulder FSW | Reduced heat input and distortion | Thin-gauge materials in aerospace |
Bobbin Tool FSW | Simultaneous double-sided welding | Hollow sections in shipbuilding |
Adaptive Control Systems | Real-time process optimization | High-volume automotive production |
Hybrid FSW processes that combine friction stir welding with other joining technologies have emerged as promising solutions for challenging applications. Laser-assisted FSW, for example, utilizes a laser heat source to preheat the material ahead of the FSW tool, enhancing material flow and enabling higher welding speeds. This hybrid approach has shown particular promise for welding high-strength steels and dissimilar metal combinations that are difficult to join using conventional FSW alone. Similarly, ultrasonic-assisted FSW incorporates high-frequency vibrations to reduce process forces and improve weld quality in materials with high melting points or low ductility. The development of multi-axis FSW systems has greatly expanded the geometric complexity of parts that can be welded using this technology. These advanced systems allow for three-dimensional weld paths, enabling the joining of curved surfaces and complex geometries that were previously challenging or impossible to weld using traditional linear FSW machines. Multi-axis FSW has found applications in the aerospace industry for welding compound-curved fuselage panels and in the automotive sector for joining complex frame structures. Innovations in FSW have also addressed the challenge of welding dissimilar materials, a capability of increasing importance in lightweight design strategies. Advanced process control and tool designs have enabled the successful joining of aluminum to magnesium, aluminum to steel, and even metal to polymer composites. These dissimilar material joints offer new possibilities for multi-material structures that optimize weight, strength, and cost in transportation applications.
Advancements in Friction Stir Welding Equipment
The evolution of friction stir welding (FSW) equipment has been instrumental in expanding the technology's applications across various industries. Manufacturers have developed sophisticated machinery that addresses the unique challenges of FSW, enhancing precision, efficiency, and versatility. These advancements have enabled the joining of a wider range of materials and geometries, contributing to the growing adoption of FSW in aerospace, automotive, and other high-performance sectors.
Modern FSW machines incorporate advanced control systems that allow for precise manipulation of welding parameters. These systems utilize closed-loop feedback mechanisms to maintain consistent force, spindle speed, and travel rate throughout the welding process. Real-time monitoring of these parameters enables automatic adjustments to compensate for variations in material properties or joint geometry. The implementation of servo-controlled axes provides smooth and accurate tool movement, resulting in higher quality welds and reduced defect rates.
The development of multi-axis FSW machines has significantly expanded the capabilities of the process. These systems typically feature five or more axes of motion, allowing for complex three-dimensional weld paths. This flexibility enables the welding of curved surfaces, contoured parts, and intricate geometries that were previously challenging or impossible to join using conventional FSW equipment. Multi-axis systems have found particular utility in the aerospace industry for welding fuselage panels, wing structures, and other components with non-linear weld lines.
Advancements in spindle technology have addressed one of the primary limitations of early FSW equipment: the ability to weld high-temperature materials. Modern FSW machines incorporate high-torque, water-cooled spindles capable of operating at the elevated temperatures required for welding steels, titanium alloys, and other high-melting-point materials. These spindles often feature advanced bearing designs and cooling systems that maintain stability and precision under extreme conditions. The increased power and thermal management capabilities of these spindles have expanded the range of materials that can be effectively joined using FSW.
The integration of process monitoring and data acquisition systems into FSW equipment has enhanced quality control and traceability. Advanced sensors measure and record a wide range of parameters during the welding process, including forces, temperatures, torque, and tool position. This data can be used for real-time process control, post-weld analysis, and documentation of weld quality. Some systems incorporate machine learning algorithms that analyze this data to optimize welding parameters and predict potential defects before they occur.
FSW Equipment Feature | Benefit | Application |
---|---|---|
Multi-axis motion control | Complex 3D weld paths | Aerospace structures |
High-torque cooled spindles | Welding high-temperature alloys | Automotive powertrain components |
Advanced process monitoring | Real-time quality control | Critical structural joints |
The development of portable FSW equipment has expanded the technology's applications beyond the factory floor. These compact, lightweight systems enable on-site welding for repair and maintenance operations, particularly in industries such as shipbuilding and aerospace. Portable FSW machines often feature modular designs that can be easily transported and assembled in confined spaces. Some models incorporate battery power and wireless control systems, further enhancing their mobility and flexibility for field operations.
Advancements in tool change systems have improved the efficiency and versatility of FSW equipment. Automated tool changers allow for rapid switching between different tool geometries, enabling the welding of various material thicknesses and joint configurations without lengthy setup times. Some systems feature integrated tool wear monitoring, alerting operators when tool replacement is necessary to maintain weld quality. These features have contributed to the increased adoption of FSW in high-volume production environments, where minimizing downtime is critical.
- Gantry-style FSW machines for large-scale structural welding
- Robotic FSW systems for flexible manufacturing cells
- Hybrid FSW equipment incorporating secondary heat sources
- Modular FSW units for integration into existing production lines
- Specialized FSW machines for specific industry applications
Future Outlook for Friction Stir Welding Technology
The trajectory of friction stir welding technology points towards continued innovation and broader industrial adoption. As materials science advances and manufacturing processes evolve, FSW is poised to play an increasingly significant role in joining applications across various sectors. The future of FSW technology is likely to be shaped by emerging trends in automation, materials development, and sustainable manufacturing practices.
The integration of artificial intelligence and machine learning algorithms into FSW systems represents a promising avenue for future development. These technologies have the potential to enhance process optimization, predictive maintenance, and quality control in FSW operations. AI-driven systems could analyze vast amounts of welding data to identify optimal parameters for specific material combinations and joint geometries, reducing setup times and improving weld quality. Machine learning algorithms could also predict tool wear and potential defects, enabling proactive maintenance and reducing production downtime.
Advancements in material science are expected to expand the range of alloys and composites that can be effectively joined using FSW. Research into new tool materials and coatings may enable the welding of ultra-high-strength steels, refractory metals, and advanced composites that are currently challenging to join. The development of functionally graded materials through FSW processes could lead to new possibilities in tailored material properties for aerospace and automotive applications. Additionally, the application of FSW to additive manufacturing processes may create opportunities for hybrid manufacturing techniques that combine the benefits of both technologies.
The trend towards miniaturization in electronics and medical devices presents new challenges and opportunities for FSW technology. The development of micro-FSW techniques for joining thin foils and small components could open up applications in areas such as microelectronics packaging and implantable medical devices. Advances in tool design and process control at the microscale will be necessary to achieve the precision required for these applications. Concurrently, research into the use of FSW for joining dissimilar materials at the micro level could enable new innovations in sensor technology and flexible electronics.
Future FSW Development | Potential Impact | Target Industry |
---|---|---|
AI-driven process optimization | 20% reduction in setup time | Automotive manufacturing |
Advanced tool materials | 50% increase in tool life | Aerospace fabrication |
Micro-FSW techniques | Joining of 0.1mm thick foils | Electronics packaging |
The application of FSW in emerging industries, such as renewable energy and space exploration, presents new challenges and opportunities for technology development. For instance, the growing offshore wind energy sector requires large-scale FSW equipment capable of joining thick-section materials in challenging environmental conditions. In the space industry, the need for lightweight, high-strength structures for satellites and spacecraft may drive innovations in FSW processes for advanced aerospace alloys and composite materials. These emerging applications may necessitate the development of specialized FSW equipment and techniques tailored to specific industry requirements.
Environmental considerations are likely to influence the future direction of FSW technology development. As industries strive to reduce their carbon footprint, the energy efficiency and minimal emissions associated with FSW make it an attractive alternative to traditional welding methods. Future advancements may focus on further reducing the energy consumption of FSW equipment and developing processes that enable the joining of recycled or sustainable materials. The role of FSW in facilitating the use of lightweight materials for transportation applications aligns with broader goals of reducing fuel consumption and emissions in the automotive and aerospace sectors.
- Development of high-speed FSW processes for increased productivity
- Integration of FSW with Internet of Things (IoT) platforms for enhanced process monitoring
- Application of FSW in additive manufacturing for large-scale metal printing
- Exploration of FSW techniques for joining metal-matrix composites
- Development of FSW processes for in-situ repair of aerospace structures
The convergence of FSW with other advanced manufacturing technologies may lead to new hybrid processes with enhanced capabilities. For example, the combination of FSW with additive manufacturing techniques could enable the production of complex, lightweight structures with optimized material properties. The integration of FSW with in-situ heat treatment processes could streamline manufacturing operations by eliminating the need for separate post-weld heat treatment steps. These hybrid approaches may offer solutions to current limitations in material joining and open up new design possibilities across various industries.
Advancements in simulation and modeling techniques are expected to play a significant role in the future development of FSW technology. High-fidelity computational models that accurately predict material flow, heat transfer, and residual stress distributions during FSW will enable more efficient process optimization and tool design. Virtual prototyping of FSW processes could reduce the time and cost associated with experimental trials, accelerating the development of new applications and equipment. The integration of these simulation capabilities with real-time process control systems could lead to adaptive FSW processes that continuously optimize welding parameters based on predicted outcomes.